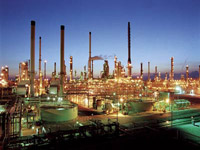
La
raffineria di petrolio
Una raffineria di petrolio è uno
stabilimento dove si trasforma il petrolio greggio, che è
una miscela
di idrocarburi, soprattutto idrocarburi
paraffinici a diverso peso molecolare, nei suoi componenti,
e dove questi ultimi vengono trattati per ottenerne altri,
che vanno da composti organici leggeri, quali il metano, GPL
(miscela di butano, propano e pentano) a composti pesanti
quali asfalti e simili.
Gli schemi di raffinazione Le raffinerie hanno un ciclo di lavorazione che può essere
classificato in funzione degli impianti presenti e dei
prodotti realizzati. Alcuni di essi sono:
 |
Hydroskimming: distillazione topping + vacuum, reforming
catalitico, desolforazione gasoli. Si realizza una bassa
resa in prodotti leggeri e un'alta resa in olio
combustibile. |
 |
Schema a
conversione:
a
differenza
delle
raffinerie hydroskimming, le frazioni pesanti non vengono vendute come
olio comustibile ma convertite termicamente o
cataliticamente in frazioni più leggere. Le raffinerie di
questo tipo sono più flessibili nel rispondere alle diverse
richieste del mercato (stagionalità dei prodotti). |
 |
Lube: in una raffineria Lube si producono principalmente
basi per oli lubrificanti. I grezzi che sono impienati
devono essere a base paraffinica. |
Gli impianti di
raffineria
Di seguito
vengono
riportati i
principali
impianti che
sono usati in
una raffineria.
Alcuni di essi
sono presenti in
tutte le
raffinerie
(distillazione
topping,
desolforazioni...)
mentre altri no.
Questo dipende
dalle
caratteristiche
del petrolio che
viene lavorato
in quella
raffineria e
dalle richieste
del mercato.
Trattamenti
preliminari
Il petrolio,
prima di poter
essere lavorato,
deve essere
separato
dall'acqua, dai
sali e dalla
sabbia che sono
eventualmente
presenti in
sospensione.
Queste
operazioni,
insieme alla
stabilizzazione
(allontanamento
della frazione
gassosa che
accompagna il
petrolio)
vengono
effettuati anche
a "bocca di
pozzo", in fase
di estrazione.
Si preferisce
ripeterli, in
maniera molto
più
approfondita,
prima di
iniziare
qualsiasi
lavorazione in
raffineria. A
causa della sua
elevata
viscosità le
goccioline ed i
solidi sospesi
non riescono a
sedimentare
spontaneamente
quindi è
necessario
operare
un'operazione di
dissalaggio. Il
petrolio viene
riscaldato in
uno o più
scambiatori di
calore fino a
50-150 °C, a
seconda della
viscosità
iniziale, allo
scopo di
diminuirla.
Questo
pre-riscaldamento
avviene a spese
di una o più
correnti di
prodotti caldi
che lasciano
l'impianto. Il
petrolio, così
riscaldato,
viene miscelato
con una certa
quantità di
acqua ed alcuni
additivi ed
attraversa una
valvola di
laminazione che
aiuta a
miscelare il
tutto molto
bene. I sali
presenti nel
petrolio passano
così in
soluzione e le
goccioline
piccole,
eventualmente
presenti,
possono
aggregarsi con
altre gocce più
grandi che
possono essere
agevolmente
separate in un
desalter. Il
desalter è una
sorta di grande
serbatoio che ha
all'interno due
piastre
elettriche. Tra
queste piastre
viene applicato
un forte campo
elettrico che
favorisce la
coalescenza
delle goccioline
d'acqua che si
separano così
dal petrolio. Il
petrolio viene
generalmente
trattato in un
ulteriore
desalter e
l'acqua oleosa
viene inviata
all'impianto di
trattamento
apposito per la
disoleazione.
Il treno di
pre-riscaldo
Il petrolio, per
poter essere
separato nei
suoi componenti,
deve essere
riscaldato e
parzialmente
vaporizzato fino
a circa 350 °C.
Questa
operazione si
effettua in un
forno e richiede
una notevole
quantità di
combustibile.
Per ridurre al
minimo il
consumo di
combustibile, si
pre-riscalda la
corrente di
petrolio
dissalato a
spese dei
prodotti caldi
che abbandonano
l'impianto di
distillazione
topping. Il
numero di
scambiatori di
calore impiegati
può essere
notevole (anche
20 o 30).
Ovviamente, per
massimizzare il
rendimento del
recupero
termico, il
petrolio
scambierà calore
con le correnti
in ordine
crescente di
temperatura,
prima quelle più
fredde e poi
quelle più
calde. Insieme
ai prodotti che
lasciano
l'impianto,
cedono calore al
petrolio anche i
"pump around"
che sono dei
riflussi
intermedi di
prodotti. Questi
prodotti vengono
prelevati,
raffreddati e
reimmessi in
colonna qualche
piatto più in
alto. In questo
modo si opera la
condensazione di
parte dei vapori
che risalgono in
colonna. Questo
insieme di
scambiatori
viene
comunemente
chiamato "treno
di scambio" o
"treno di
pre-riscaldo".
La distillazione
topping
Il greggio è una
miscela molto
complessa di
idrocarburi che
non può essere
impiegata
direttamente.
Necessita
innanzi tutto di
essere separa in
frazioni (o
tagli
petroliferi)
tramite
l'operazione di
distillazione
topping (o
atmosferica). I
tagli
petroliferi sono
miscele di
idrocarburi che
hanno una
temperatura di
ebollizione
compresa in un
determinato
intervallo. Le
frazioni che
otteniamo da una
colonna di
distillazione
sono
generalmente:
 |
Incondensabili
(C1 +
C2) |
 |
 |
GPL (C3
+ C4) |
 |
Benzina
(C5 ÷
C9) |
 |
Kerosene
(C9 ÷
C12) |
 |
Gasolio
leggero
(C13 ÷
C14) |
 |
Gasolio
pesante
(C15 ÷
C20) |
 |
Residuo
atmosferico
(C20+) |
Il
petrolio
dissalato e
pre-riscaldato,
viene alimentato
in un forno che
lo porta fino ad
una temperatura
di 350 °C circa.
La carica,
parzialmente
vaporizzata,
viene immessa
nella zona di
flash della
colonna (sul
fondo) dove
vaporizza
ulteriormente in
virtù di una
riduzione di
pressione (si
passa da 5 bar a
2 bar). Tutti i
prodotti che
hanno una
temperatura di
ebollizione
inferiore sono
vaporizzati e
risalgono verso
l'alto mentre i
prodotti più
pesanti (residuo
atmosferico)
escono dal
fondo. La
corrente
gassosa, man
mano che sale in
colonna, viene
in contatto con
il liquido che
scende dai
piatti di
ditillazione
superiori. In
questo modo
condensano prima
i prodotti con
la temperatura
di ebollizione
più alta. Da
alcuni piatti di
distillazione
sono prelevati i
prodotti che poi
vengono inviati
alle lavorazioni
successive. La
corrente liquida
che scende è
costituita dai
pump around e
dal riflusso
(portata di
liquido) immesso
in testa alla
colonna.
La distillazione
vacuum
Il residuo topping contiene ancora altri composti che
possono essere utilizzati ma la loro temperatura di
ebollizione a pressione atmosferica è così elevata che
subirebbero una rottura se li si vaporizzasse a pressione
atmosferica. Questo processo si chiama cracking termico. Per
ovviare a questo inconveniente si distilla il residuo
topping ad una pressione notevolmente inferiore (40 mmHg
circa). Il residuo Topping viene riscaldato in un forno
nuovamente fino a 380 °C ed immesso nel fondo della colonna
vacuum. I prodotti ottenuti dipendono dal tipo di grezzo
utilizzato e sono, nel caso di grezzi paraffinici per
lubrificanti:
 |
Gasolio
da vuoto
(VGO) |
 |
3
frazioni
lubrificanti
leggere
e medie |
 |
Residuo
da vuoto
(asfalteni
+
frazione
lubrificante
pesante) |
Nel caso di grezzi per la produzione di combustibili:
 |
Gasolio
leggero
da vuoto
(LVGO) |
 |
Gasolio
pesante
da vuoto
(HVGO) |
 |
Residuo vacuum (asfalteni) |
I gasoli da vuoto possono essere utilizzati per alimentare
le navi oppure per produrre benzine e gasoli per
autotrazione tramite dei processi di cracking termico o
catalitico.
I prodotti della distillazione vengono di solito inviati ai
trattamenti di desolforazione, in cui si inietta H2 che
viene poi separato in forma di H2S (acido solfidrico) e in
seguito ridotto, nei classici impianti per il Processo Claus,
a zolfo elementare. Dalla distillazione sotto vuoto si
ottengono quindi i prodotti pesanti, quali gasolio e olio
combustibile.
Questi prodotti non sono subito utilizzabili
commercialmente, perché spesso non rispettano tutte le
specifiche come il numero di ottano o il contenuto di zolfo.
Inoltre è improbabile che le quantità prodotte rispettino le
proporzioni delle quantità vendute. Si sono quindi
sviluppate nel tempo delle tecniche di processo mediante le
quali le molecole di idrocarburi pesanti vengono spezzate in
molecole più leggere - ad esempio mediante una reazione del
tipo C13H28 + H2 -----> C7H16 + C6H14
Questi processi sono detto processi di cracking
(letteralmente: spezzettatura) e consentono, nel caso
indicato, di ottenere una molecola di eptano ed una di esano
(cioè due di benzina leggera) partendo da una molecola di
C13, ossia gasolio.
Si pone evidentemente anche il problema inverso : greggi
molto leggeri possono dare un eccesso di benzine a scapito
dei gasoli. Sono stati allora sviluppati dei processi di
reforming (letteralmente: riformatura), inversi di quelli di
cracking.
Attraverso tutti questi trattamenti di ottengono, nelle
quantità desiderate, tutti i prodotti che il mercato
richiede. Tra questi, si distinguono le frazioni pesanti
(C20 e oltre), che hanno poco interesse commerciale e che
vengono spesso usate in raffineria per produzione di energia
in speciali caldaie, e soprattutto la virgin naphta, già
citata, che è la principale materia prima per l'industria
petrolchimica, e quindi per la produzione di materie
plastiche, gomme sintetiche e di un'infinità di materiali
diversi.
Schema del processo di raffinazione: dalla distillazione
atmosferica (topping) si ricavano i vari tagli di benzine
successivamente lavorati in impianti specifici. Le frazioni
più pesanti vengono lavorate in una colonna sotto vuoto (vacuum)
dove si recuperano altri combustibili.
Schema del processo di raffinazione: dalla distillazione
atmosferica (topping) si ricavano i vari tagli di benzine
successivamente lavorati in impianti specifici. Le frazioni
più pesanti vengono lavorate in una colonna sotto vuoto (vacuum)
dove si recuperano altri combustibili.
La
torre di frazionamento
La torre di frazionamento è composta da una torre cilindrica
in acciaio alta circa 30 m e larga 3,50 m. All’interno della
torre ad intervalli regolari si trovano dei piatti
orizzontali forati, muniti di appositi passaggi, alcuni dei
quali sormontati da coperchi detti campane di gorgogliamento.
La temperatura della torre è elevata alla base e va
diminuendo con l’altezza. Il petrolio che entra alla base
della torre è preriscaldato in un forno fino a 360°C. I
componenti che hanno punto di ebollizione inferiore a quella
temperatura, salgono la torre sotto forma di vapore.
Incontrando i piatti e le campane di gorgogliamento che sono
al di sotto della temperatura di ebollizione, condensano e
si depositano sul piatto allo stato liquido. Apposite
tubazioni possono raccogliere queste frazioni liquide e
allontanarle dalla torre. Le frazioni ad elevato punto di
ebollizione che non evaporano entrando nella torre, si
spostano alla base e, data l’elevata temperatura, passano
allo stato aeriforme e, condensando, si raccolgono sui
piatti inferiori.
La raffineria e l'ambiente
Una raffineria di petrolio è certamente un impianto
industriale con forte
impatto ambientale, sia per l'area che essa normalmente
occupa,
misurabile in ettari, sia per la grande componente
energetica - quasi tutti
i processi di raffinazione sono di tipo termico - sia per
l'effetto sull'ambiente.
In tempi recenti le tecnologie di raffinazione hanno ridotto
di molto gli scarichi liquidi e gassosi; oggi è possibile
vivere vicino ad una raffineria senza seri problemi
sanitari. Tuttavia, le emissioni, pur ridotte, non sono
annullate, e le grandi dimensioni di questi impianti fanno
si che queste emissioni, piccole se considerate
relativamente, siano comunque importanti in termini
assoluti.
D'altra parte, le raffinerie sono un tassello essenziale
nella filosofia di
vita attuale. Se è quindi giusto operare per un sempre
minore impatto ambientale della raffineria, si deve pur
sempre tenere conto che nessun processo, fisico o chimico,
può mai lasciare inalterato l'ambiente che lo circonda.
La
costruzione di nuove raffinerie nei paesi occidentali è
stata ferma per quasi vent'anni: ciò è probabilmente dovuto
al fatto che le compagnie petrolifere attendevano
l'imminente picco del petrolio che avrebbe fatto calare
drasticamente il consumo di idrocarburi e rendere gli
impianti attuali sovrabbondanti rispetto alle necessità di
produzione. Nel periodo tra il 2004 e il 2006, invece, si è
avuto un netto aumento degli investimenti sia in nuovi
impianti che nel miglioramento di quelli esistenti.
Nel 2007 è partita la costruzione della prima raffineria
grass roots negli Stati Uniti d'America dopo quasi un
ventennio - a Pascagoula, TX, ed è in corso il rifacimento
totale o parziale di un gran numero di raffinerie. La causa
di ciò risiede probabilmente nell'elevato costo del greggio,
che consente alle imprese di raffinazione di compiere
ingenti investimenti (una raffineria completa, nel 2006, ha
un costo dell'ordine di 1 - 2 miliardi di Euro), realizzando
così economie di processo e di scala. |